Deep Dive Into the Electrical Product Certification Process
Below is a transcript of this video clip.
00:00 We're going to go a little bit deeper dive on the application and documentation review.
00:09 I mentioned this already with the annuals portion of it. Certification is not just a one-time thing. It's not a one and done process, and then you dust your hands off and move on, you're good to go. We document everything up front that goes into this product to ensure what is it being made out of, what components are being used, how are they constructed, and how does this product operate? And not just any one product, but the entire product line. If you submit a series of 10 products for testing or certification, we need information on all 10 of those products to make it informed decision on what we have to test.
00:48 And that way, it's a big information gathering up front, but we can then identify the one or two models to test, maybe more, depending on the situation, that will then verify all products comply with the standard.
01:02 It's better than testing everything. It's a big documentation hurdle, but it really is a much lower cost and better from a timing perspective, because then we're testing fewer things because we have ensured that we're testing the worst-case representative.
01:18 The documentation that we need kind of group these into buckets here, the first being the components lists or parts lists, (it may be called the critical component lists). And this is something that needs to be representative of all your products in the line being certified. So not just the largest, not just the smallest, not just the one you make the most of. All models must be represented by this parts list.
01:44 And then we need a breakdown of how these models vary, are different or the same, both at a component level and performance and electrical rating level. So we need to get pretty granular and also a big picture of how these are different or similar.
02:03 And then something that's a little bit more routine, as far as this what's the ask: manuals, installation, operation, safety and data plates. Those are requirements within the safety standards. I always encourage manufacturers to read the safety standards because they will have very prescriptive requirements on what information needs to be contained, where it needs to be contained, the size of it. It's very important information. So please read those safety standards to make sure you check all the boxes on what's required.
02:24 Additionally, French language manuals and labels. If you're certifying for a Canadian standard, it must have labels and manuals in both English and French. Canada is a dual language country, so this is a requirement.
02:54 And then lastly, wiring schematics, product drawings, diagrams: we need this so that way we know how this product works and functions. We have all the components on the parts list. We're able to identify concerns between models, on maybe their wire, maybe the safety hazards. And that way we can better have an understanding of what makes this product work. How does it function? And yes, we're confident in the models that we've requested for testing will cover all of the products in the family.
03:29 What exactly goes into this component list? It's a pretty beefy list. Generally, the bill of materials is a close analogy. It's not exactly that, but it's close. The bill of materials often will have things that we don't need, think of packaging requirements, as far as it puts in a box, it's got foam around it. We don't need that, but pretty much everything that's related to the electrical components, the enclosures, grounding, gasketing, labels. We need to know all that. So it's pretty close to the build materials.
04:03 I can't give a one-to-one, this needs to, every single component that needs to be on there, because it's impossible. There's too many types of products. There's too many variations to how manufacturers build their mouse track. So I can't give a detailed one-to-one, but you are the product expert, you know all the components, you give that information to us. And then we confirm and verify through reviewing the wire and schematics through review of your product diagrams, through review of your operation installation manual. That way we know, yes, indeed, everything has been told to us about what is going into this product that we care about.
04:41 And it needs more than the billing materials, that line of number two there. Bill of materials typically are just your part number, maybe your vendor number, and the description of the component. We need a lot more information about the components to verify their ratings, where you're buying it, what component you're buying, what's the supplier, what's the manufacturer. Is it certified or recognized? If so, to what standards? We need a lot more information than just a typical bill of materials.
05:10 And also we need to know alternate vendors and alternate components. If you're buying power supplies from two different locations, we need to know that. If you're buying multiple gauge wire, we need to know that. If it's a model difference, maybe one model uses one component and another model uses another component for the same purpose, we need to know that too. So it's really a very detailed list of all of your products being certified that needs to be documented in this component list.
05:39 Also the PCD, if it's not certified, or if you're making your own, we want to know what goes into that. What components you're using into that as well. So it's a very detailed breakdown. And probably the most important beyond just getting us a list of all those components, is the certification status of all the components, absolutely critical. These safety standards for the nationally recognized standards for the United States and Canada, need components that are certified or recognized for appropriate applications. So this is critical. "If it's CE labeled, it's good." Not necessarily. Do you have the test reports for that? Does it have certification to the United States standard? We need that information and you should find it. And if you don't know, ask us so we can help figure out where you might be able to find that information. It is absolutely critical and it definitely will slow your process down or potentially require a lot more testing if you are unsure or are using uncertified components.
06:41 So again, the bill of materials isn't quite enough, as far as the information provided. So what are we looking for when we have a component list? The component description: it's a power supply, it's a Raceway, basic stuff like that. We also need the trade name. What are you buying it as? What is the invoice look like? When is called out on there for what the component is not your internal part number, what's the paperwork behind it that says we bought this part number. Supplier, where are you buying it from? And if it's different, the manufacturer of that component, we want to know your distributors, but we also need to know who makes that component, if you know. And also the ratings of that component. Wattage, amperage, IP rating, we need to know that as well. And then again, I'm going to reiterate this, certification specific information. What standards is this product certified to? Is it rated for something? Give us the listing number, give us the data sheet that calls out the standard.
07:42 And I did say I can't give you a list of all the required components that need to be on your parts list, but these are a few examples. The cables and wiring, both power supplies, gaskets, enclosures, labels, the PCB and/or the components of raceways, lights, safety stops, buttons, switches, motors, grounding kits, grounding logs, tanks, you name it. We need all of it.
08:13 So I put together a very generic example of what a component list would look like. It's five line items and pretty small. It doesn't really make a lot of sense, but this will be typically many, many, many lines long.
08:26 For most of our products that we see that get certified. But includes the component description, the supplier and manufacturer, the trade name, and then the ratings. So for example, if you have a plastic enclosure, maybe a plastic tank. We would want to know who's making that plastic tank, or if you're molding it yourself, we need to know who the manufacturer of the resin is, the name of the tank if it's a finish good, or the name of the resin you're using to mold that tank. And then the certification number or listing number and the flame rating of that material. And if you don't know, leave it blank but provide the technical data sheets that you do have so we can review and evaluate it, so maybe we can find that information. But also we will ask as well, if you leave it blank, we'll try to follow up with you to make sure, have you checked in to it? Do you know? Because it'll save time if you can get that information upfront.
09:20 Data plates. We do need to know that those have to be certified as well. So we do ask, who are you buying your data plates or your labels from, and are those labels certified.
09:31 Cabling and wiring. In this example, the supplier manufacturer are left blank. Typically we can allow variations and sources and any supplier for example, but we need to know specifics on what you specify, in the gauge certifications you require before we can allow any supplier designation on a parts list. And it's all very component specific.
09:59 Now the last two line items, I've got power supply for model one, power supply for model two. And this example, this parts list is represented by at least two models being certified. And they happen to use different power supplies. I've documented that on here as model one and model two. You can see the trade names are different between them. For a power supply, we would need to know a lot of information. The watts, the voltage, amperage, the IP rating, and also we would need the recognition details, such as the conditions of acceptability. So you're not going to be able to put all those conditions of acceptability in a nice Excel sheet, but you would need to have the supporting documentation for that component to send to us for evaluation. So you have a see attachment, for example, and you would send that to us. Because those are critical for evaluating these components and their use in your end product.
10:58 And besides a total breakdown of a component list, we're looking at a model-by-model comparison, also critical. Because that way we have a side-by-side view of, we know exactly, if we ask for model one, what's going to be in it? If we ask for model two, what's going to be in it? Is it the same? Is it different? If we need to test one particular component over another, we're accurately requesting the model that uses that particular a component.
11:22 And then we can bracket and technically justify testing some models over others, and why we don't have to test everything. So this is really important to have that side-by-side comparison. And I've given a little Excel example down here at the bottom. This can come in many different ways and formats really knowing which models use what components, however it's easily and clearly able to convey that information will work for us.
11:49 Sometimes that's even verbally or quick email or a statement or two. Because maybe it's very few differences or very simple differences. So really this is just an example, but we have to have this so that way, when we get audited by our accreditors, we can justify, we've tested this particular model. It covers the certification of all these other models, and here's why. We can technically document can justify that.
12:20 So there's the deep dive into the component list. That's really a big lift up front, as far as getting all that information. When working with NSF, you have an account manager, project manager that you work with directly. They're the best resource for working through what exactly you need to provide, questions and answers on that. But once you've gotten that documentation in and it's been reviewed, let's move on to the next steps of the certification process.
12:47 Which is the construction review, the safety test, the initial production inspection, the initial facility audit, listing, and then your annual requirements.
13:01 So I've kind of lumped these into three main gates. So there's multiple steps on that process. There were five, but there's three major gates or phases to get through after that documentation review, before you get certified.
13:16 The first being that construction review. We actually would have a physical sample or samples in our testing lab, and we're evaluating the design and construction requirements of the product against the performance standards to be certified against. This is looking at, making sure your manuals and data plates have the appropriate information in the right locations and the right letter size. That the product has the appropriate warning labels inside if there's live components. It's making sure the stickers that are on there are certified and they're legible, and they don't peel off. Is there correct spacing between high voltage and low voltage? Is there correct shutoffs for when things are opened or closed? Are there barriers, or insulating barriers if there are live wires inside the equipment?
14:09 We also are looking for the grounding. Is the grounding there? Is it acceptable? And we're looking at the overall design of the product as well. Does it have certified components? Are those components certified for the appropriate application and end use? This is all the design and construction phases, entailing, and a lot more that are standard specific. And we do this first again, because if we catch something here, that means it's easier to make a change now, and more cost effective than if we've gone through, done all the performance testing, and then you have to go back, make a modification, and redo that performance testing. So it's a much easier change now and a much lower cost change now at this design and construction review.
14:56 Are there any nonconformances for this construction review? Maybe you have a non-recognized power spot. Maybe you don't have the appropriate grounding. Those corrective actions are issued to the manufacturer, and those changes must be reviewed and evaluated before moving on the next phase, which is the actual safety testing. This is the nitty gritty, the performance testing to make sure this product is safe, and it's not going to be a fire hazard to the end user zero. It's not going to create other types of hazards. The standards detail all the requirement tests. Those are typically temperatures, dielectrics high pots, grounding checks, any abnormal testing. If something were to fall onto a component, would it catch fire? Would it dent? Would it leak?
15:47 There's also end location specific testing. If you're certifying a product for a wet environment or a splash area, we actually will do rain tests or splash tests to make sure this product is safe for those applications.
16:03 And then it's just like the construction phase. If there are nonconformances in the safety testing, all of those must be addressed re-evaluated. And depending on what the corrective action is, retested. Either in the same product with a modification, or a new product, to ensure the product complies with all of the requirements of the standard.
16:24 And then once we pass the safety testing, we move on to the audit, the initial production inspection. This is a very important step. And we do this step last, because if there have been any changes to your product through that construction process, that safety performance testing process, that way we don't have to go and redo the facility audit as well.
16:47 So again, these are done in series. So that way, if there's an issue, we don't have to redo anything. It may seem like it's longer, but ultimately this is a much smoother process, it saves time, and it definitely saves cost in redoing and rework on some of these.
17:03 In that initial audit, we're looking for: Are you using the components in your production facility that you've told NSF? Have you changed any of them? Is there maybe something you haven't told us about. Maybe there's models that you want to certify that you haven't told us about in a product line. We also check for complaint record keeping. We check for quality assurance systems to make sure that you have those in place. We're verifying that you have the appropriate production line testing. Those are all standard specific, so I'm not going to go into what those all are, but those are required on all equipment that are being certified. So we would verify you have the equipment place and their procedures in place to do it.
17:43 And it's also for the initial audit, it's an informational audit as well as a verification audit so that way you know what's required of you going forward with the certification process and how you maintain your certified product.
17:56 And then we also check, are you using the NRTL mark appropriately? You can't put the mark on yet or not yet certified, but during that audit and during the construction review as well, in both times we verify you have the appropriate mark and it's being used in an appropriate way as sort of a draft setting. This way you're ready to use it appropriately once you've been certified.
Electrical Product Compliance for the U.S. and Canadian Markets
Electrical Field Evaluations
Ready to Begin the Process?
Contact us with questions or to receive a quote.
How NSF Can Help You
Get in touch to find out how we can help you and your business thrive.
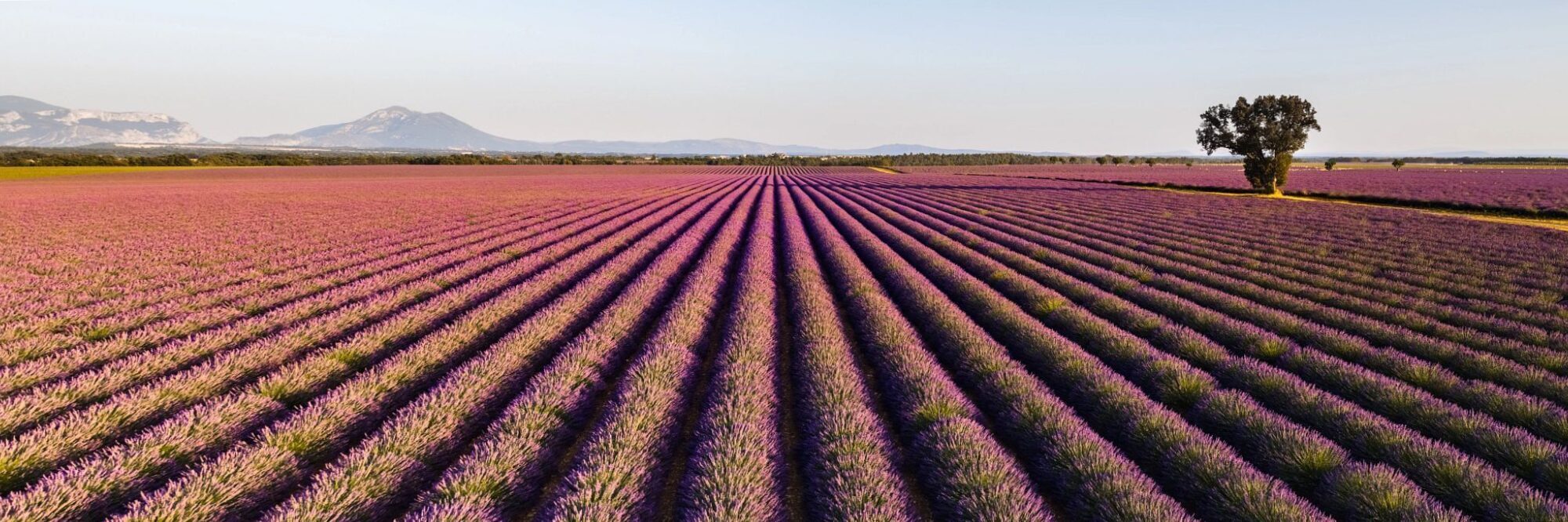
What’s New with NSF
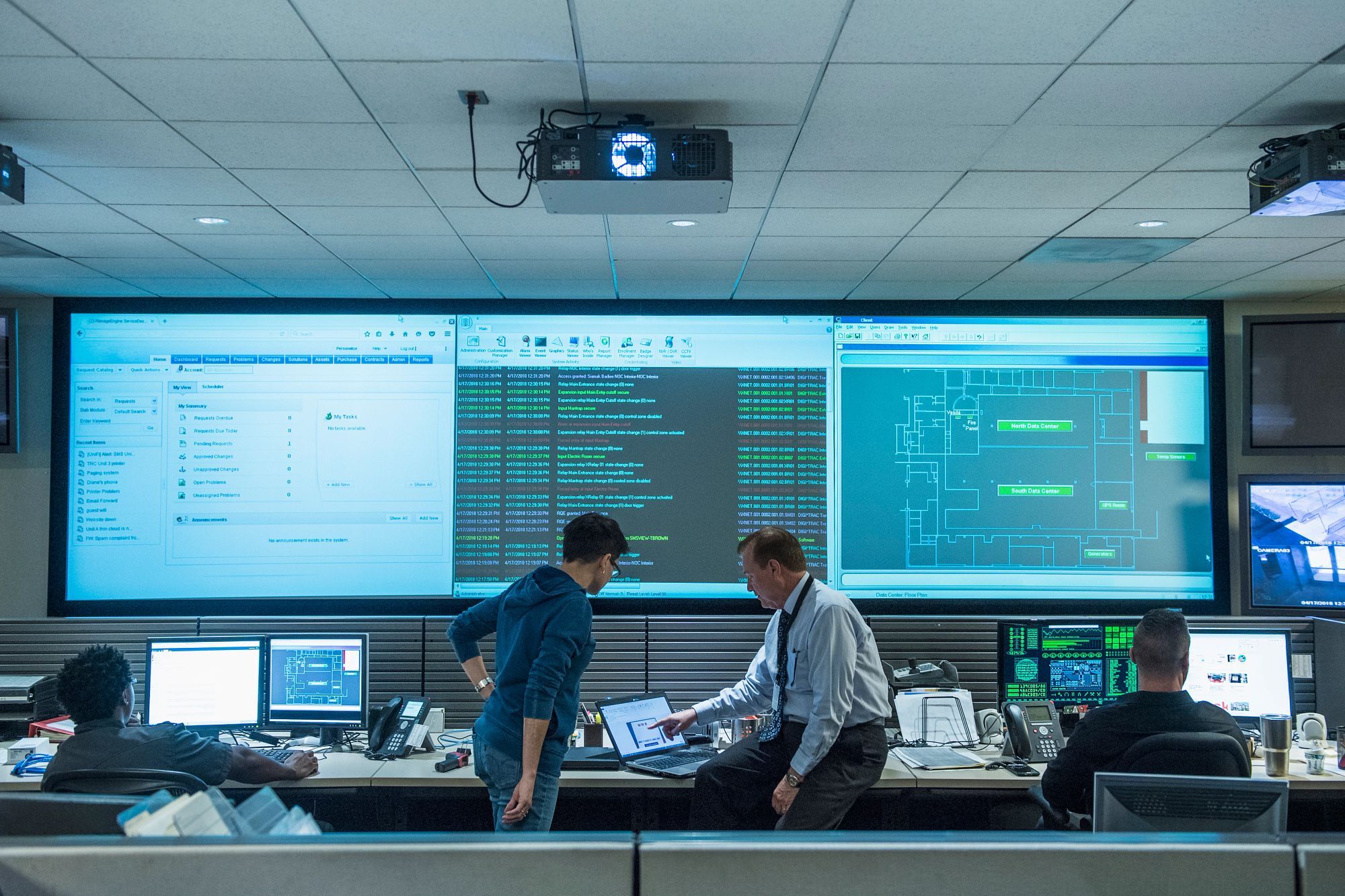
NSF Granted Reauthorization as a CMMC Third-Party Assessment Organization
January 8, 2025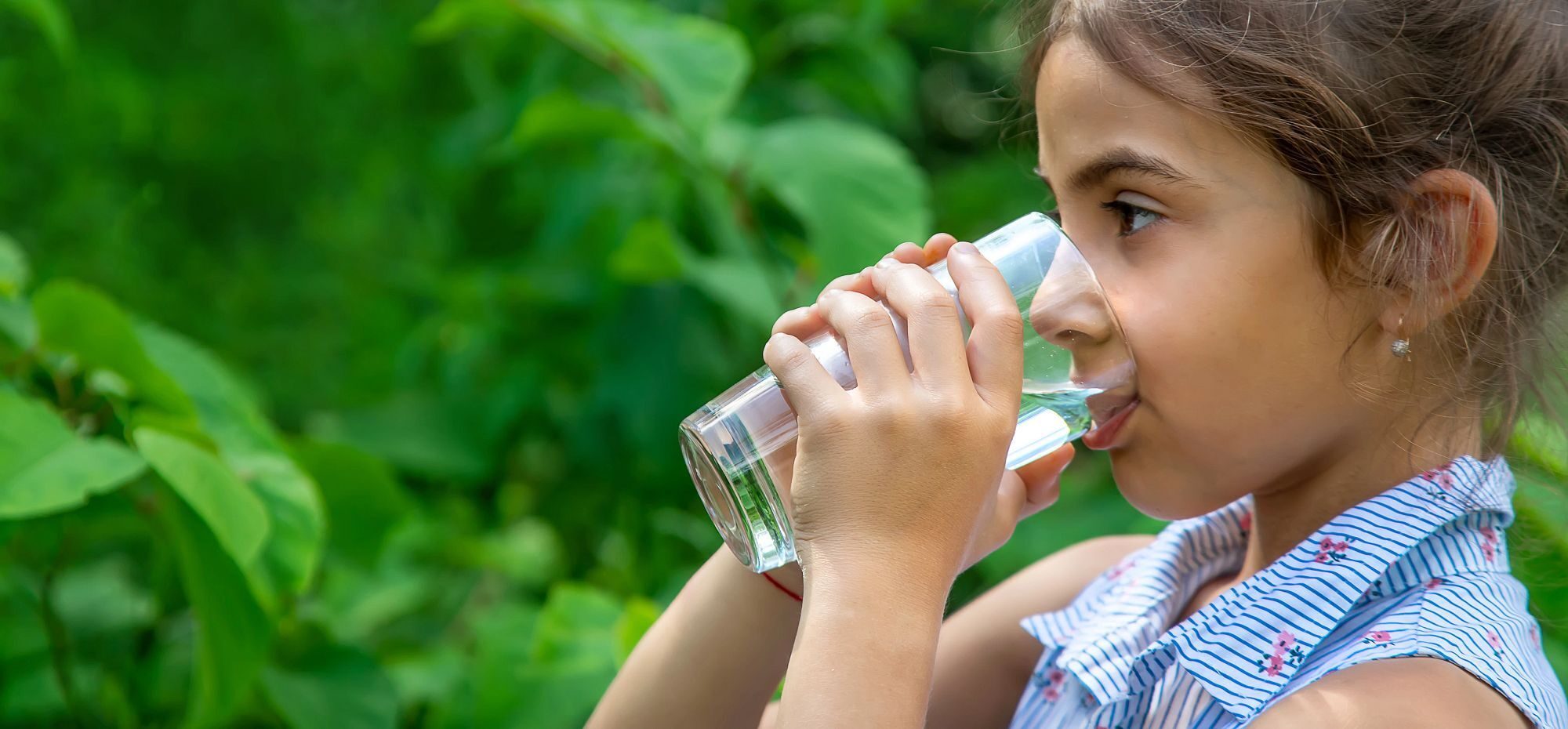
NSF Celebrates 50 Years of the Safe Drinking Water Act
December 16, 2024