Driving Logistic Excellence With Grupo Jumex
Grupo Jumex is a leading Mexican brand specializing in the production of fruit and vegetable juices and nectars. Founded in 1961, the company expanded rapidly in the internal market and, since 1982, also to the United States and other countries. Currently, Grupo Jumex holds the largest share in the domestic market and is present in 23 countries on all continents. Its 12 production plants utilize 18 different fruits and vegetables, which make up a portfolio of more than 500 products.
The challenge
In Mexico, Grupo Jumex relies on an extensive supply chain of 77 distribution centers. In 2019, the company decided to separate the quality management from its logistic operations, in order to raise the level of customer service and reduce costs related to four types of losses:
- Products rejected by customers due to quality defects that were undetected during loading
- Destroyed or damaged products due to mishandling or lack of compliance with specifications during storage and loading
- Charges or losses due to lack of control and compliance with the FIFO (First In First Out) inventory method
- Reworks and losses due to lack of an effective maintenance plan for equipment and facilities
To achieve these goals, Grupo Jumex sought the support of NSF’s extensive experience in the field of food safety.
The solution
NSF developed a three-year program, from 2020 to 2022, to integrate the logistics of 60 distribution centers into the company’s quality system. The project was structured in three phases:
a) A training program on Good Warehousing Practices (GWP), document control, and HACCP principles for food safety. Centers with high volume and export activities also received training on SQF (Safe Quality Food) certification, a food safety and quality standard recognized by the Global Food Safety Initiative (GFSI). Training was conducted through e-learning and in-person methods, achieving an 87% attendance.
As José Carlos Mejía, Head of Quality Assurance and Distribution, explains, “The intrinsic skills of the leaders at each distribution center were the main challenge we faced initially. We had graduates, accountants, and specialists from administrative areas, but not with specific skills to address quality issues.”
b) The development of documentation for standardizing different logistic operations, such as:
- GWP Manuals
- Manuals for handling finished products (FP) in logistics operations
- Procedures for traceability, rotation, withdrawal, and operation specifications
- Self-assessment and system improvement processes
c) Development of an auditing and continuous improvement process to assess the operations of each distribution center under the same quality framework, track corrective action plans, and issue Certificates of Conformity at the end of the process. Audits were designed with three different levels of standards: basic, intermediate, and certifiable, based on the size and complexity of each distribution center.
According to José Aurelio Calzada Pérez, Quality Assurance Manager, “Our experience during the audit process was very positive. NSF auditors were always very professional and doing truly constructive work. I see the audit process as a continuous improvement and learning process. In a way, the auditor is your teacher. So, we were able to learn how to review and elevate our standards according to best practices.”
The results
Thanks to the implementation of the quality system, Grupo Jumex achieved a substantial improvement in several logistics indicators: “Thanks to NSF’s support, we were able to standardize the different processes and operations we had throughout the entire supply chain, and this helped us improve significantly in terms of losses, service levels, and customer service,” says Mejía. “We also improved the culture of the staff towards product care and safety, always seeking the highest attention to detail from reception to delivery to the customer and fostering healthy competition among different distribution centers.”
The most significant KPIs (Key Performance Indicators) certifying the success of the project were:
- Customer service level exceeding 95%, with no rejections or returns due to quality issues
- 45% reduction in destructions due to mishandling
- Average audit rating score exceeding 85.10
- Closure of non-conformities raised during the audit within a maximum of 30 days
- Implementation of the FIFO method within the quality system, with a potential 90% reduction in expired products
The quality assurance project has concluded successfully. However, the collaboration between Grupo Jumex and NSF continues: “We want to continue working with NSF on training our internal staff and our supplier base, as well as on the recertification audits of our distribution centers,” says Calzada Pérez.
“NSF has been our auditing home for more than ten years and has always stayed at the forefront of different safety and quality systems. If we want to be the best, we need to work with the best, and from our perspective, NSF has always been the best,” says Mejía.
How NSF Can Help You
Get in touch to find out how we can help you and your business thrive.
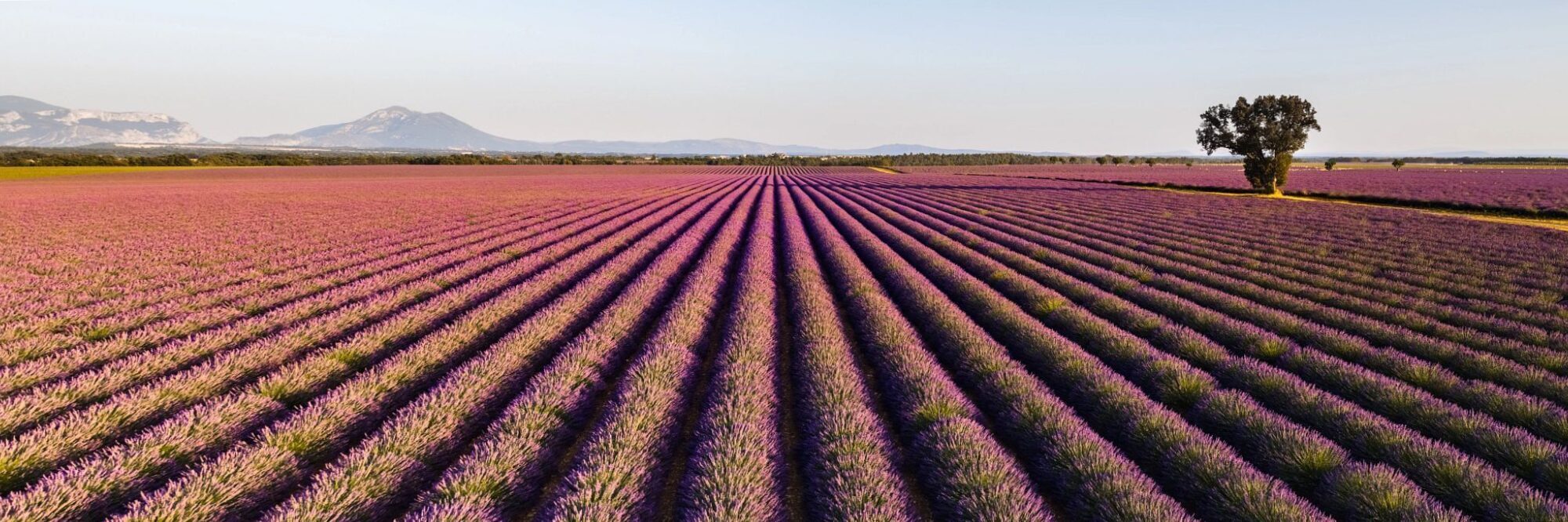
What’s New with NSF
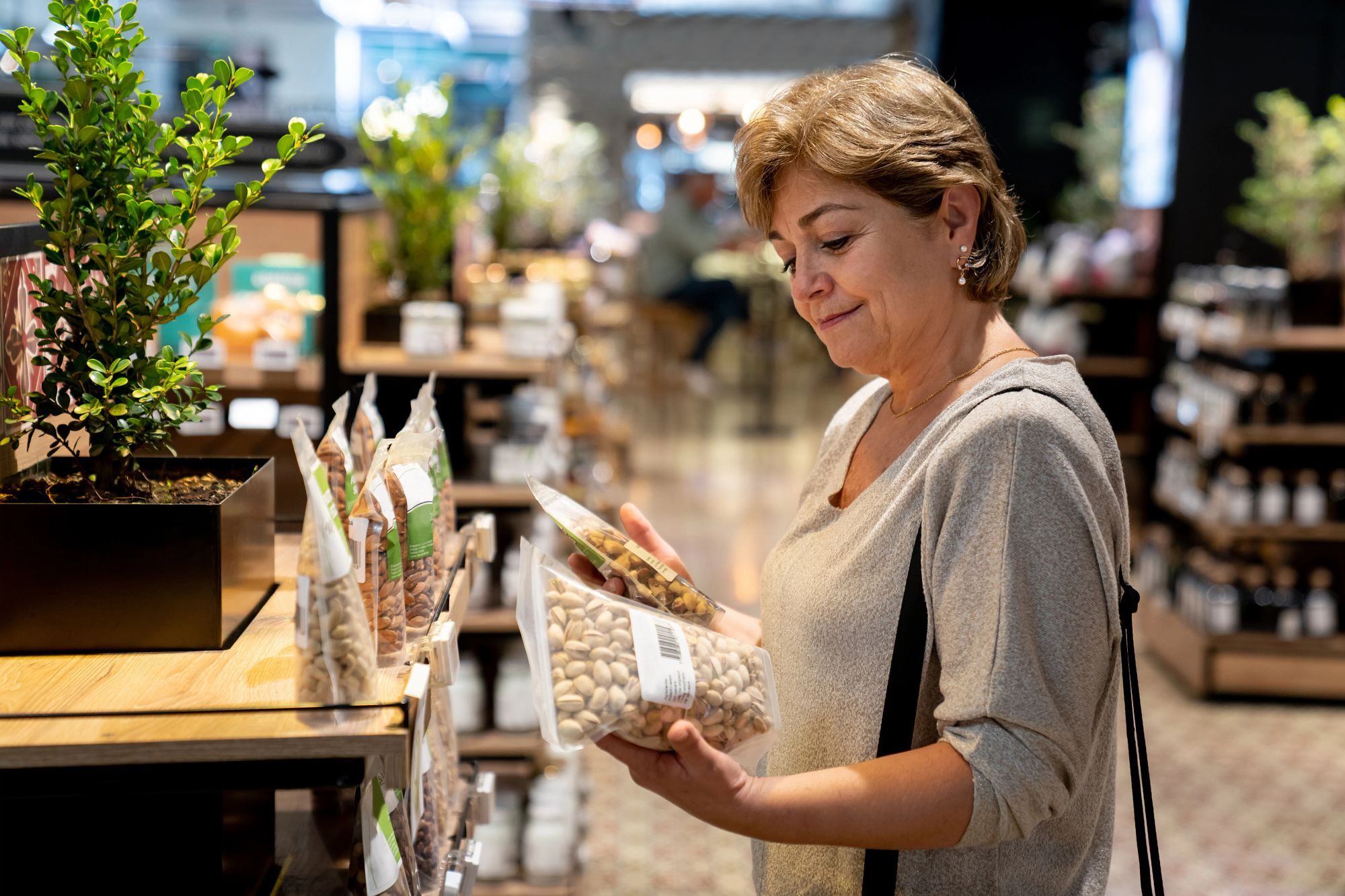
NSF Research Reveals Brits Demand Greater Clarity, Transparency and Standardisation in Food Labelling
January 8, 2025
Brooklands New Media’s Publication On NSF’s Global Animal Wellness Standards (GAWS) Not Endorsed by NSF
November 25, 2024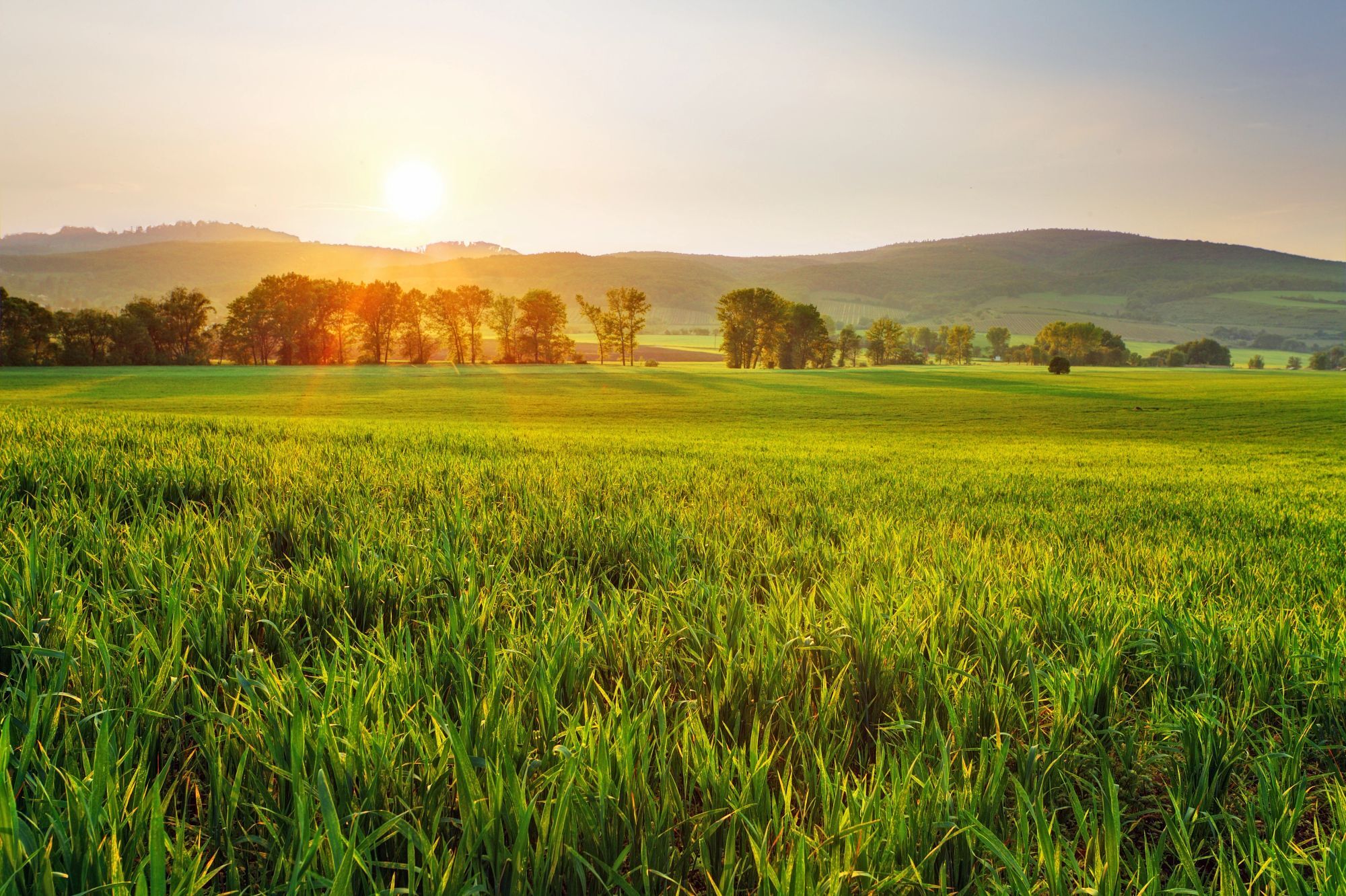