Unlocking Success: Best Practices for Manufacturers Under the FDA’s New LDT Rule
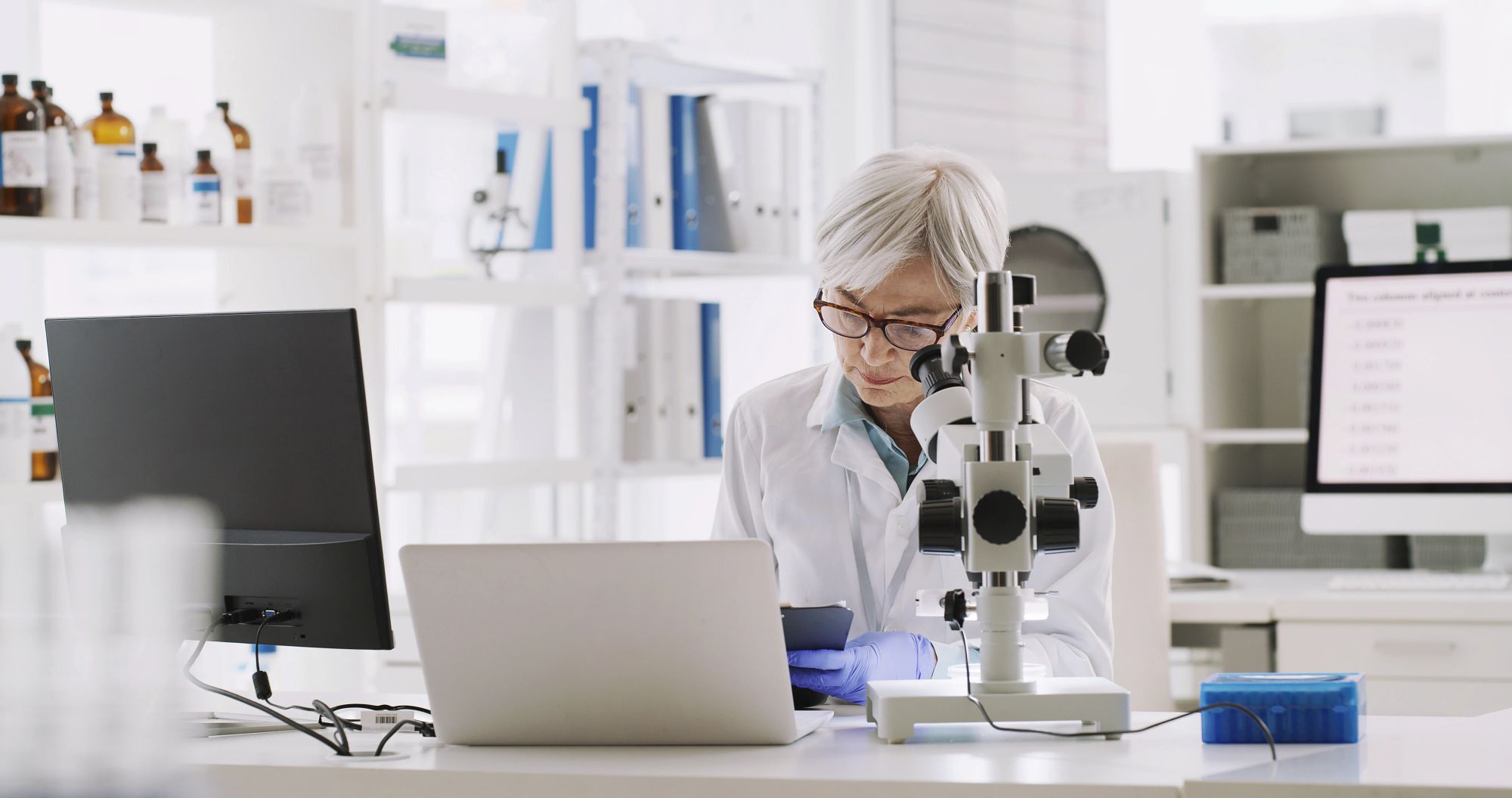
The U.S. Food and Drug Administration (FDA) has introduced a groundbreaking rule aimed at regulating Laboratory Developed Tests (LDTs) as medical devices. For manufacturers selling LDTs in the United States, this represents a significant shift requiring careful attention and strategic planning to ensure compliance. This article distills insights from NSF experts Janet Book and Jacob Foster, who shared critical strategies for navigating this new regulatory environment in a recent webinar.
Understanding the new rule
Historically considered services rather than products, LDTs are in vitro diagnostic tests produced and used within a single laboratory. The FDA now classifies LDTs as medical devices, subjecting them to regulation under 21 CFR Part 820. The new rule will be implemented in stages, with full compliance required by 2028. The initial focus is on medical device reporting requirements, recall procedures, and complaint handling systems—all pivotal for ensuring patient safety and maintaining regulatory alignment.
Phase one compliance: key challenges
The first phase of implementation centers on establishing compliance with medical device reporting requirements. For manufacturers, this involves adapting to rigorous systems for recalls and complaint handling. The sheer variety and complexity of LDTs make this an intricate task.
NSF’s experts emphasize the importance of developing robust complaint handling procedures. Manufacturers must analyze complaints systematically, identifying root causes and trends to implement corrective actions effectively. Such efforts are critical not only for regulatory compliance but also for safeguarding the accuracy and reliability of the tests.
Data analysis: a cornerstone of quality management
Janet Book and Jacob Foster stress that comprehensive data analysis is fundamental to ensuring LDT quality. By aggregating and scrutinizing data from multiple sources, manufacturers can uncover recurring issues and implement preemptive measures. This approach supports compliance while enhancing the credibility and market appeal of LDTs.
For manufacturers, this means investing in systems capable of capturing, managing, and analyzing complaints and performance data. Identifying trends and implementing corrective actions based on these insights can reduce liability risks and enhance the overall reliability of products.
Consumer and business protection
The new FDA rule underscores the dual responsibility of protecting consumers and business interests. Quality assurance is no longer optional; it is a regulatory necessity. Manufacturers must establish comprehensive quality management systems that not only meet FDA requirements but also build trust with end-users.
From a business perspective, aligning with the new regulation protects against potential liabilities and reputational harm. Effective compliance systems reduce the risk of recalls and associated costs, ensuring a smoother pathway to market for new LDTs.
Implementing corrective actions
Effective corrective action procedures are another critical focus area. Root cause analysis—a systematic method for identifying the underlying causes of problems—must be integrated into every manufacturer’s quality management system. Statistical techniques and well-reasoned sample selection are essential tools for maintaining compliance and ensuring the continued reliability of LDTs.
Enhancing operational efficiency
The transition to FDA-compliant systems also presents an opportunity to optimize operational efficiency. NSF experts recommend integrating incremental improvements into existing processes to avoid disruptions. These enhancements can strengthen the efficiency of quality management systems, driving long-term benefits for both compliance and business performance.
How NSF supports LDT manufacturers
Navigating this regulatory shift requires expert guidance. NSF offers a suite of services tailored to LDT manufacturers, including training in quality management system development and gap analysis. These resources are designed to empower manufacturers to meet FDA requirements while enhancing their operational capabilities.
NSF’s approach focuses on collaboration. By partnering with manufacturers, they ensure solutions are sustainable and integrated seamlessly into existing workflows. This proactive approach minimizes compliance risks and positions businesses for success in a more regulated environment.
Preparing for the future
The FDA’s regulation of LDTs as medical devices represents a transformative shift for the industry. By approaching compliance strategically, manufacturers can not only meet regulatory requirements but also improve the reliability and effectiveness of their products. Investing in robust quality management systems and data analysis tools will be essential in navigating this complex landscape.
Manufacturers should view this as an opportunity to enhance their market position. Compliance with the FDA’s new rule will not only protect against regulatory penalties but also demonstrate a commitment to quality and patient safety—key differentiators in a competitive market.
Conclusion
The pathway to compliance with the FDA’s new rule on LDTs may be challenging, but it is achievable with the right strategies. By focusing on robust complaint handling, data analysis, and quality management systems, manufacturers can ensure compliance while strengthening their market position.
NSF stands ready to support LDT manufacturers through this transition, offering the expertise and resources needed to succeed. By preparing for each phase of regulatory change, manufacturers can turn compliance into a competitive advantage, ensuring their LDTs remain trusted and effective in the evolving healthcare landscape.
Other NSF LDT readiness recommended resources
We have compiled other articles on the issue of FDA’s new LDT rule to help you and your colleagues.
Navigating New FDA Regulatory Terrain for Laboratory Developed Tests (LDTs) This white paper provides an in-depth exploration of these changes, offering actionable strategies and comprehensive insights to help LDT providers navigate and adapt successfully to these significant changes.
Ready to begin the process?
Get in touch with our NSF experts to find out how we can help you and your business thrive.
What’s New with NSF
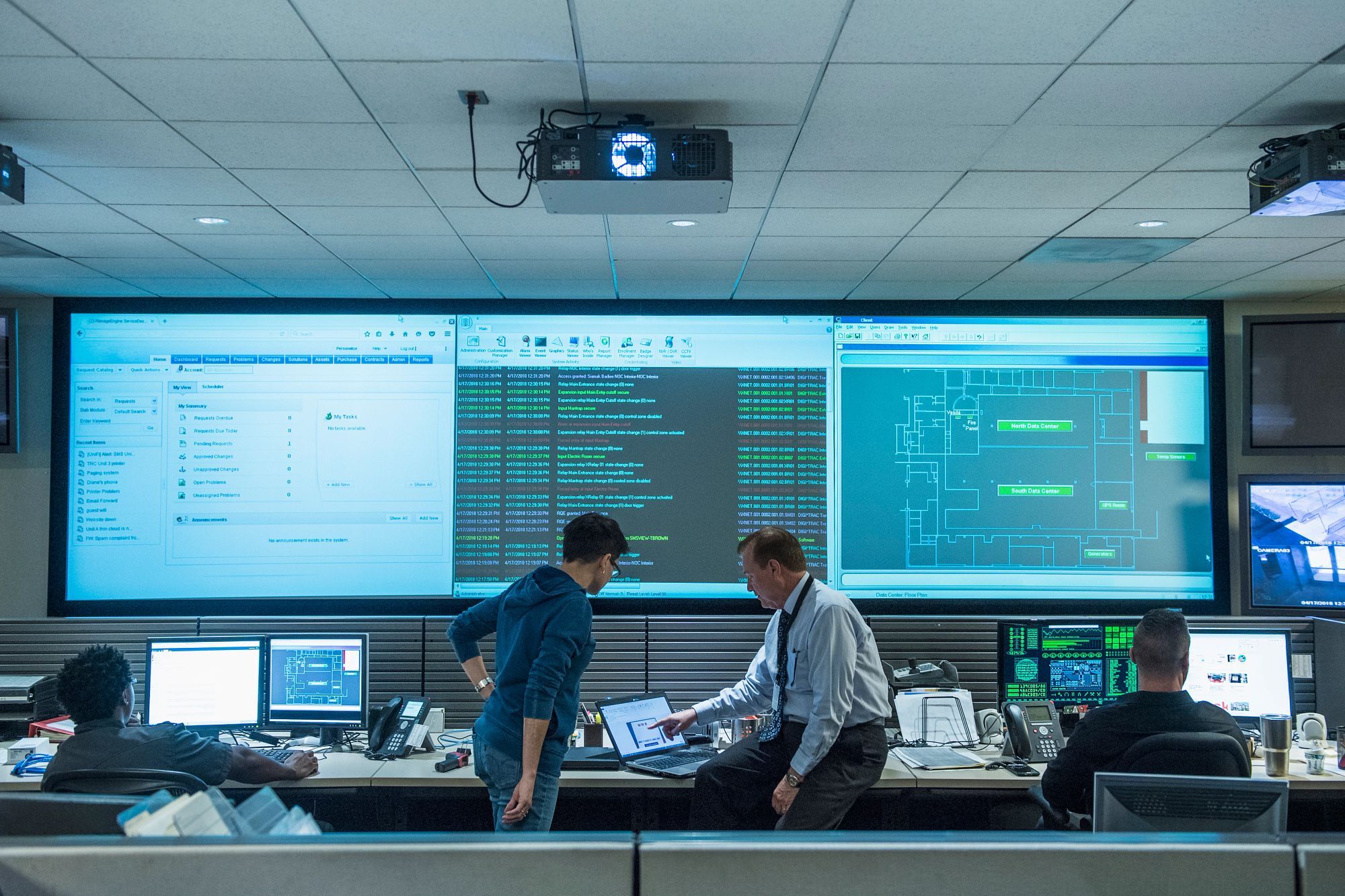
NSF Granted Reauthorization as a CMMC Third-Party Assessment Organization
January 8, 2025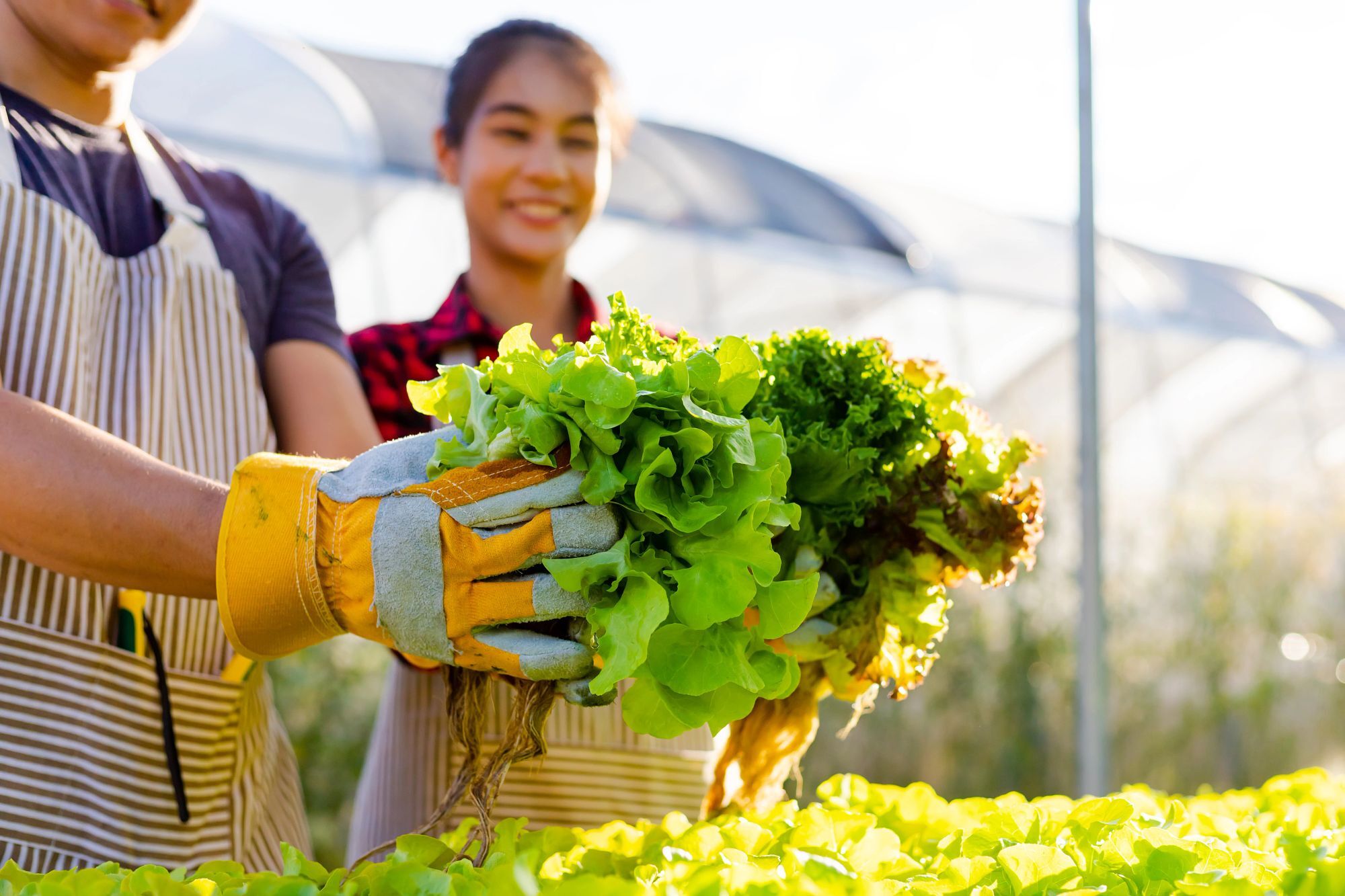
Sustainable Foods Summit 2025
January 2, 2025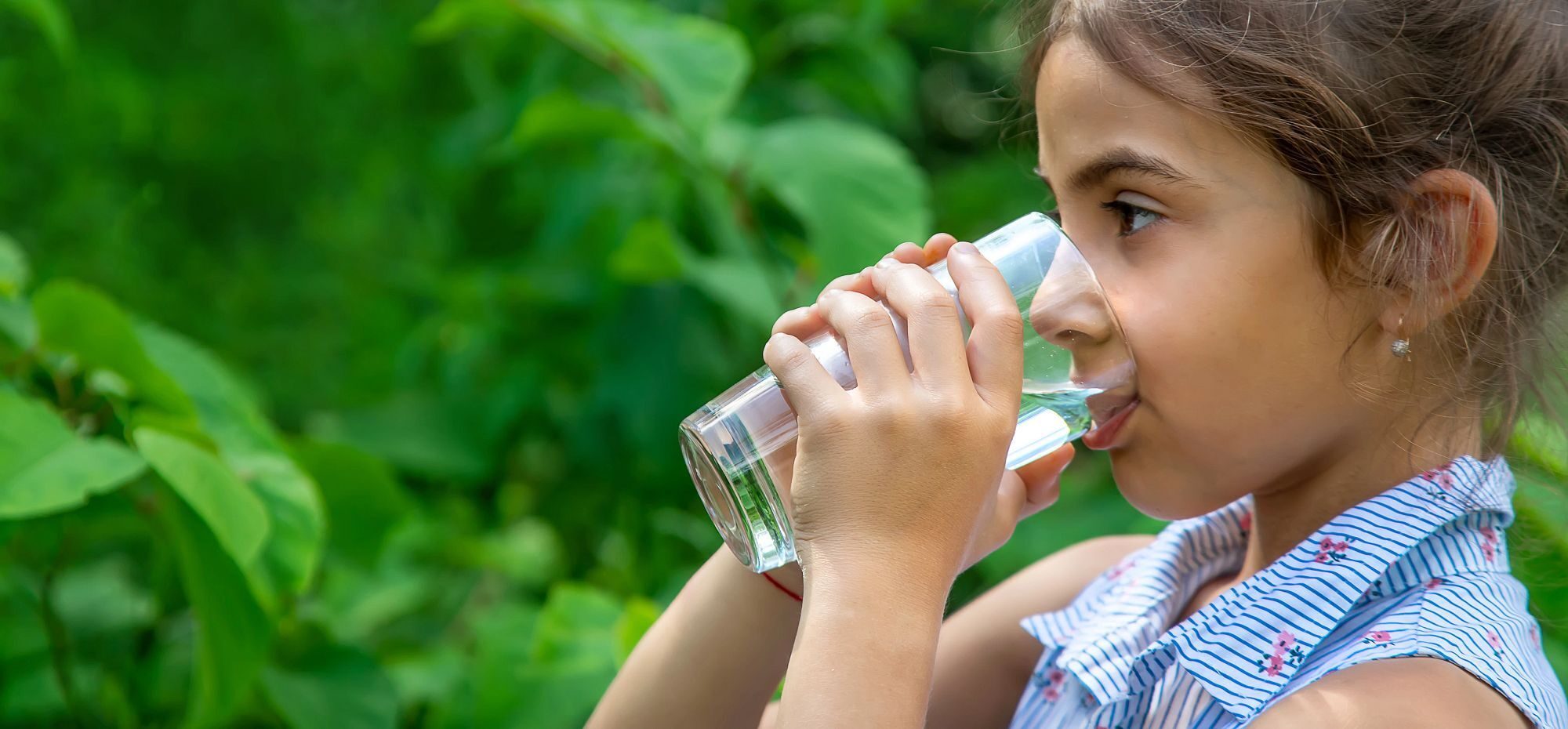
NSF Celebrates 50 Years of the Safe Drinking Water Act
December 16, 2024