How Disinfectants Can Influence Material Selection in Plumbing Products
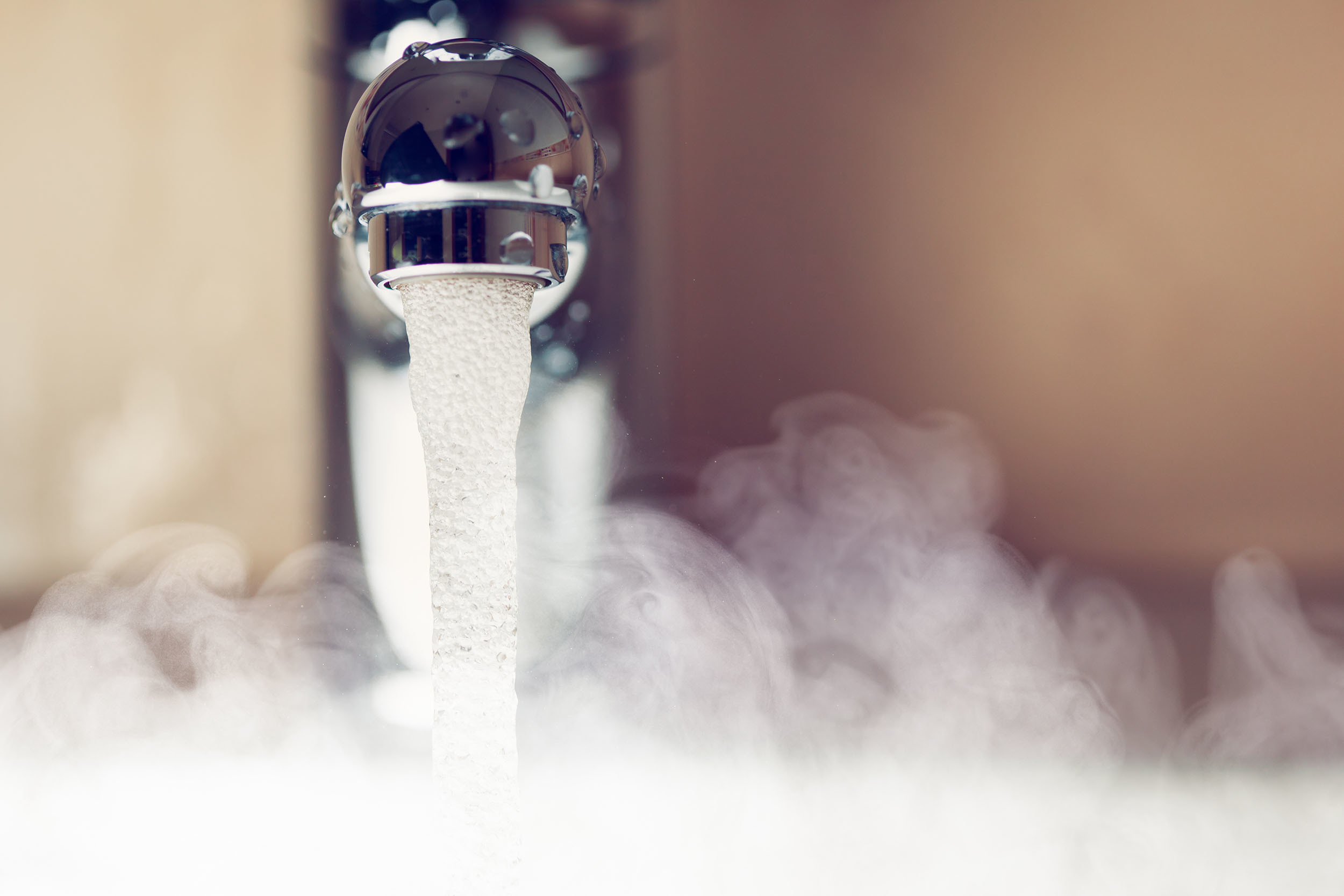
Material selection plays a critical role in developing a finished plumbing product as it impacts design, cost, in-service performance and regulatory approval. To ensure a quality product, a manufacturer’s decisions throughout the development cycle should include considering the end-use application.
One key aspect of potable water end-use applications for plumbing products is the impact that disinfectants, chloramines or hypochlorous acid (chlorine) have on a material. Each disinfectant affects materials differently, so understanding their impact in service is critical when making final material and design decisions.
Impact of Disinfectants
Chloramines typically degrade elastomers to a greater extent whereas the effect of chlorine is typically greater on thermoplastics. As both materials are often found in plumbing components, it can be beneficial to test the effects of each of these disinfectants on those product types. As an example, chlorinated water preferentially attacks higher stress areas of a part and can highlight potential issues with stress concentrations or knit lines. Flow-through testing of a product with these disinfectants in a potable water environment can give insight into the potential oxidative degradation of the product in-service. By contrast, immersion (static) testing of the materials does not replicate either the flow patterns or the disinfectant replenishment observed in service.
How Test Methods Are Developed
Resistance to chloramines and chlorine is typically evaluated to an ASTM standard, such as ASTM F2023 or ASTM F2263, that was originally designed for piping. However, these standards can be applied as a starting point to plumbing components that are either behind the wall (valves, waterways, etc.) or in front of the wall (supply lines, faucets, etc.). Both these ASTM methods use elevated temperature to accelerate the oxidative reaction in the test chamber, where hours in the test chamber can be translated into years of service for a part. Additionally, the test chamber operates continuously whereas a faucet, for example, is used intermittently, so a usage acceleration factor for plumbing components can often be applied – for example, if a faucet is on 15 minutes a day, then 24 hours of testing is equivalent to 96 days of use). This potentially reduces test times even further relative to service.
We can develop test methods for specific plumbing product types under an accelerated rate and elevated temperature to determine how they will perform in potable water applications containing common disinfectants.
Key Takeaways
Oxidative testing is often combined with post-exposure sustained pressure testing. Comparing the performance of an unexposed component to one that has been exposed to chlorine or chloramines allows observing the change due to oxidation. With pressure testing components, after various intervals in the oxidative resistance chamber, a profile of the potential impact of oxidative degradation as the part ages can be achieved. Using testing to understand the impact of potable water disinfectants can provide insight into the in-service performance of a material. This can result in an improved design and quality for a plumbing component.
Interested in Learning More?
How NSF Can Help You
Get in touch to find out how we can help you and your business thrive.
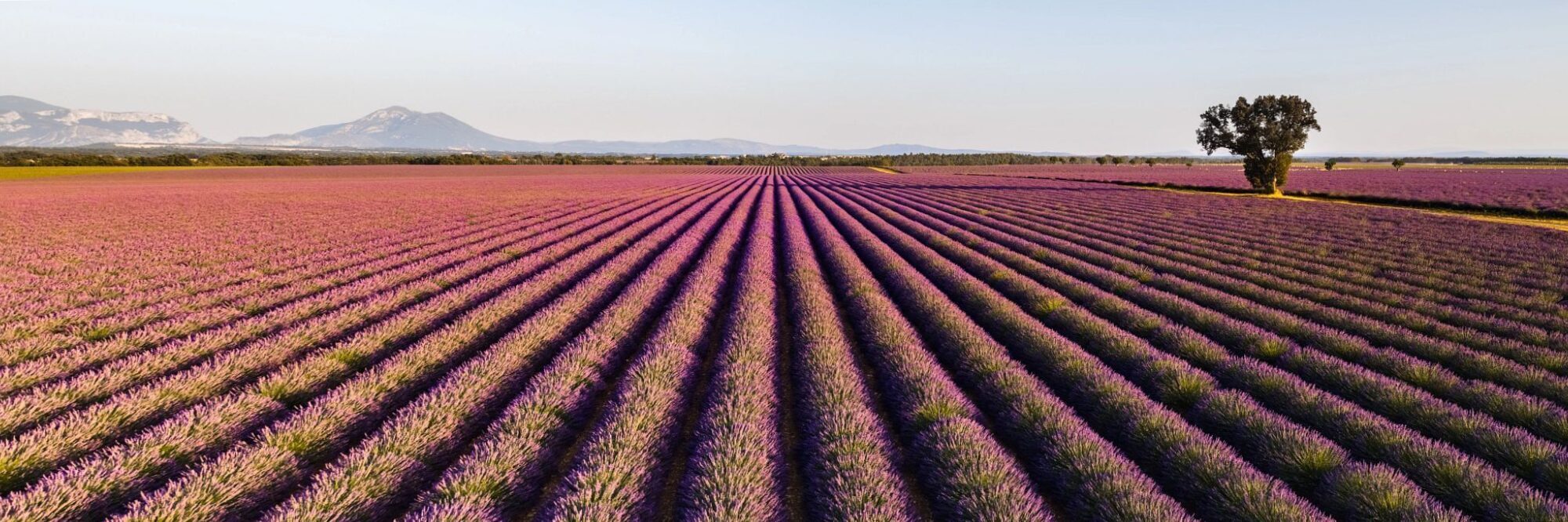
What’s New with NSF
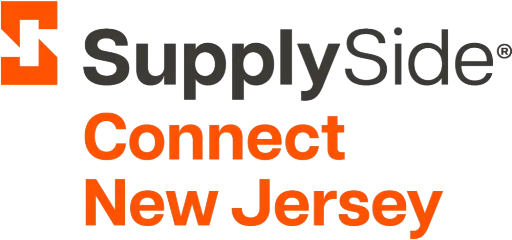
GMP and Regulatory Compliance Virtual SupplySide Connect New Jersey Training
January 30, 2025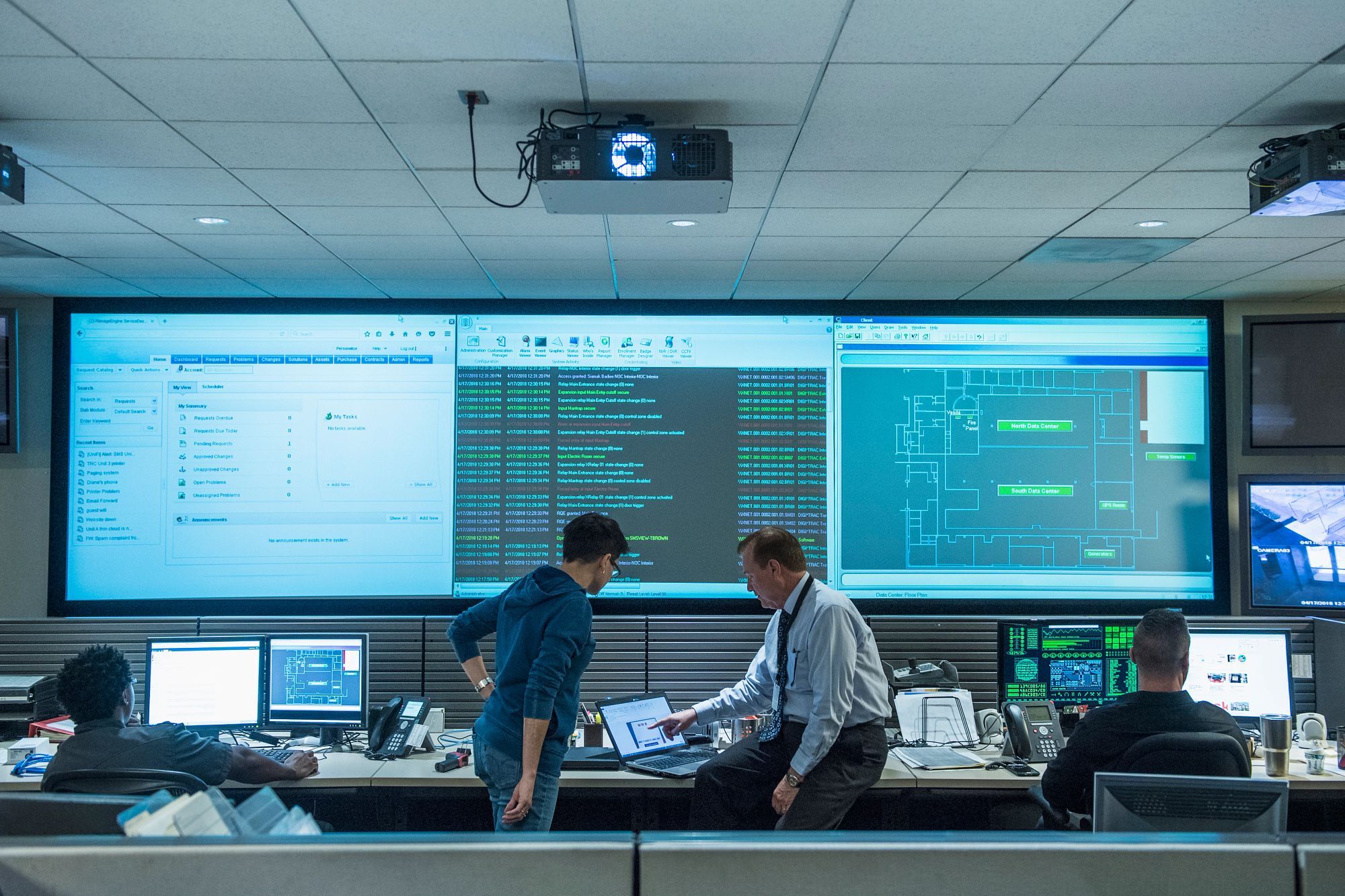
NSF Granted Reauthorization as a CMMC Third-Party Assessment Organization
January 8, 2025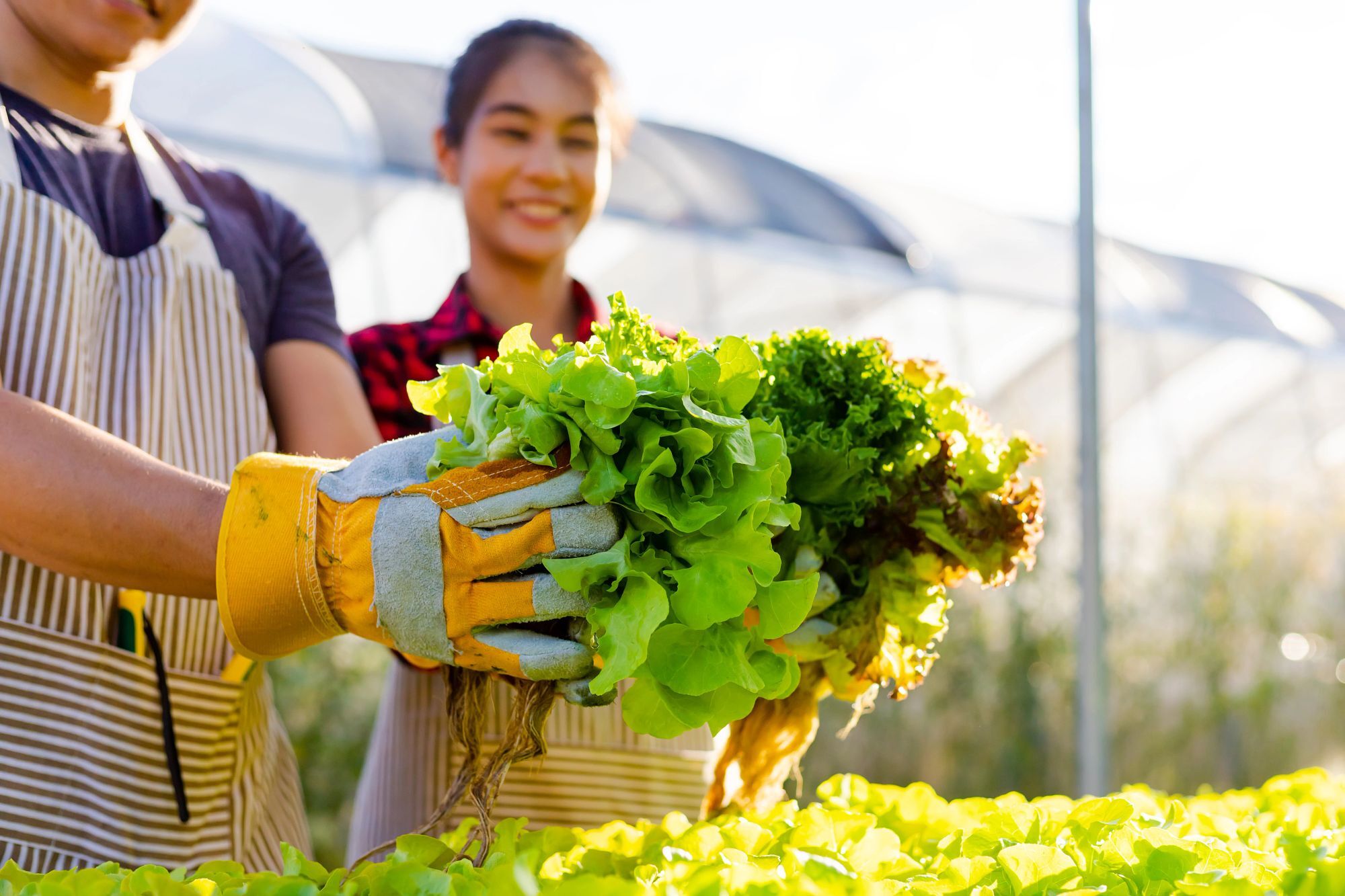
Sustainable Foods Summit 2025
January 2, 2025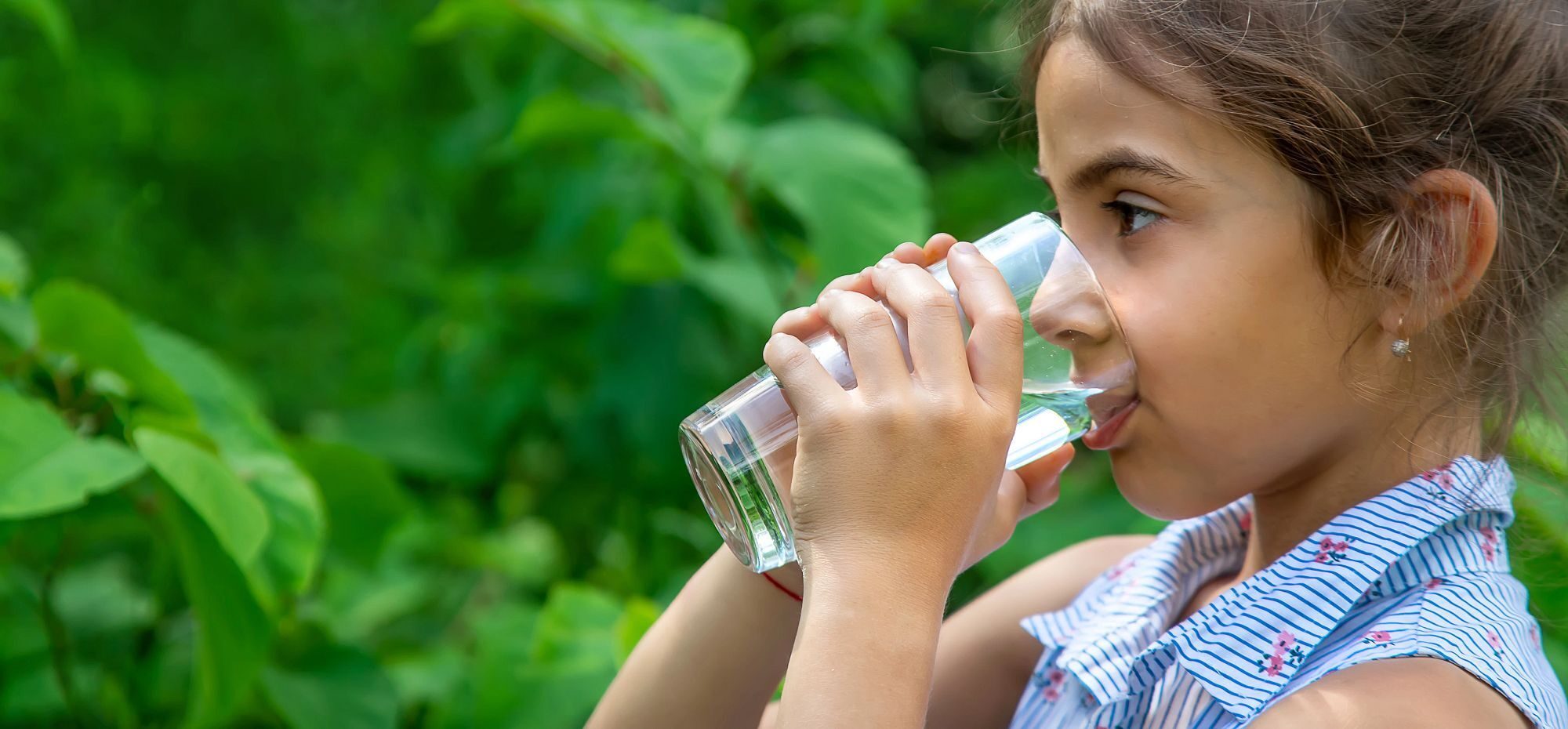